Bicycle power meters are typically accurate within ±1% to ±2%, but accuracy depends on proper calibration, installation, and environmental factors.
Understanding Accuracy in Cycling Power Meters
Cycling power meters have become a revolutionary device for any athlete, providing real-time data previously unattainable to their users. Where the value of these devices ultimately lies is in their accuracy, as no training regime or competition strategy can be devised and executed effectively without it. Generally speaking, the accuracy of power meters is measured as a percentage, most commonly presented as a deviation from the true power output. As with most other precision devices, high-quality power meters’ accuracy is within the range of ±1% to ±2%.
The Main Factors Affecting Accuracy
The inaccuracy and variance of power meters can and do depend on several factors. The primary one is calibration, as readouts of any measuring instrument should be correspondingly precise and accurate. However, several other complex aspects come into play. These are environmental and mechanical variables such as changing temperature, drivetrain wear, and others that are compensated for in various power meter innovations. Modern devices utilize auto-calibration features to mitigate the impact of such factors and may also be outfitted with temperature compensation firmware, allowing them to perform more accurately in varying conditions.
Different Power Meter Designs
Power meters come in several forms, all of which experiment with distinct measuring methods. Hub-based systems are made to interfere with the bike as little as possible, although their simplest version is relatively heavy. Their accuracy typically lies in the range of ±1%. Crank and pedal meters are also capable of measuring the left-right balance, but their options can require more frequent calibration. Some of these options accurately measure the power output within the ±1% range.
Practical and Reliability Information
Ultimately, a power meter’s effectiveness in the real world will depend on its reliability. However, it is not perfect discrete accuracy that athletes and their coaches are interested in. In measurable terms, repeatability will matter far more. Some devices will remain within the same range despite environmental or mechanical shifts — an important factor for athletes and coaches, given the unpredictability and chaotic nature of any cycling scenario.
Factors Affecting Power Meter Readings
When assessing the reliability of power meters, it is essential to understand the elements that impact their readings. As precise as they are, these instruments do not function in a vacuum. Instead, they come into contact with a plethora of variables, each of which can push the measurements in one direction or another.
Calibration and Installation
Proper calibration and installation are the cornerstones of exact power measurement. A power meter that is not correctly calibrated or featured is capable of showing deviations of more than 5% from the true power output. This step is crucial; even the most sophisticated instrument can fail if the setup is not perfect. For that, riders should follow the manufacturer’s instruction to the letter and conduct calibration checks regularly, especially before the major training session or race.
Temperature Variations
Temperature not only has a significant impact on overall comfort but is also essential for understanding power meter reading. If not specifically designed for temperature compensation, many power meters may shift its accuracy by up to 2% for each 10°C shift in ambient temperature . This is because the strain gauges and electronics located inside the meter react differently to various temperatures, changing the device’s sensitivity and hence precision.
Drivetrain Efficiency and Wear
The efficiency of a bike’s drivetrain and its overall worn status play an important role in power meter accuracy. Studies indicate that a dirty drivetrain or a chain near the end of its lifespan can result in a power loss of 5-10 watts, which the power meter does not account for and offers as part of the output . Regular maintenance and cleaning of the chain and cogs ensure that the power meter output is as close to the actual pedal power as possible.
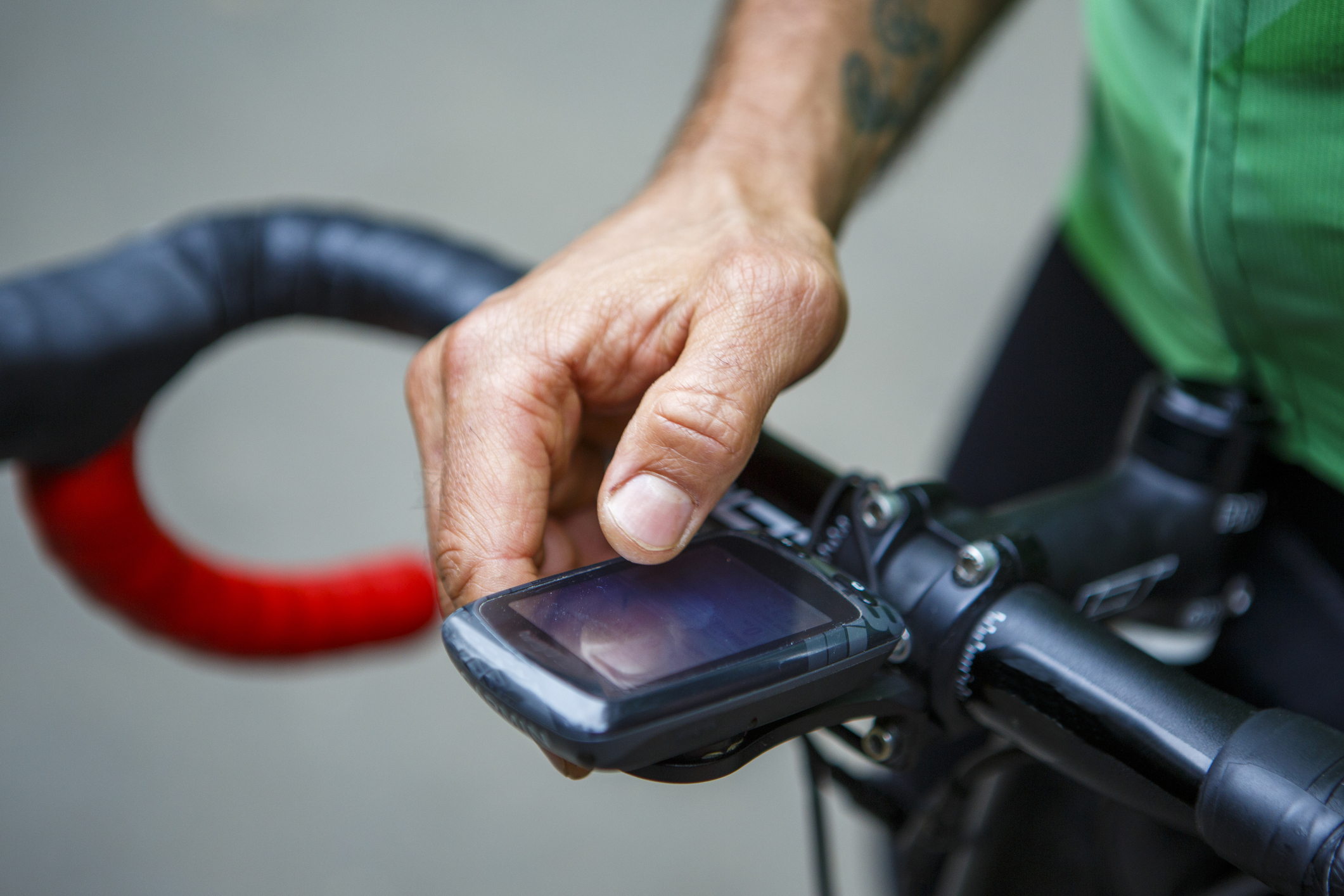
Rider Position and Dynamics
It is an interesting fact that the way the rider sits or pedals can affect the power meter data. Sudden changes in riding position or cadence lead to short-term spikes or drops in power outputs. Hence, it is important to maintain a consistent riding style and position, although the majority of power meters are aimed at reducing these discrepancies through advanced algorithms or data smoothing options.
Determining Power Meter Reliability
In the fierce pursuit of peak performance, cyclists see power meters as indispensable devices in both training and racing. However, how can you be sure that your power meter is providing the truth? There are many factors to consider when determining the reliability of these devices, and it is pigheadedly more complex than reading a percentage on an online speaker’s spec sheet.
Consistency of a Source of Power Through Time
The deliverance of similar readings of your power meter on a cold, rainy day and a hot, sunny day demonstrates a reliable power meter. Always ensure that you are comparing identical work efforts when testing, such as a structured workout that you have previously completed with the same instructions but in different conditions. Bad calibration or outdoor power meter reliability will drift well above the desired 1-2% range. This is a straightforward way of determining the reliability of a source of power.
Comparative Data Analysis
The third and highly effective way of measuring the reliability of a power meter is by comparing it with a source you can trust, i.e., a high-grade indoor trainer. The data sources have similar precision, as those from power meters are calibrated precisely. Ensure that you include a 2-3% measurement error and a more considerable margin taking into account user error. Some power meters estimate power output significantly higher than a few remaining trustworthy indoor trainers.
Data Over Time
The power meter reliability is not only singularly defined by your current sense of power. It also relies on when the data was recorded. For a more accurate reading, be sure to look at the more extended lapse of time. A more extended window or detailed checks spanning months or years may give you beneficial insights into a power meter’s reputation. If a meter changes throughout, yet no changes are made inside, potentially a calibration or power meter’s lifespan is made.
Key Steps in Assessing Power Meter Damage
For cyclists who rely on precise data tracking to monitor their performance and progress, maintaining a power meter’s accuracy and reliability is essential. However, accidents happen, and when they do, knowing how to assess damage to your power meter is a critical skill. The following series of steps is designed to help you evaluate the physical damage it may have sustained and determine whether it can still provide reliable power data.
Visual inspection
The first step is to closely examine the power meter in question. Look for apparent signs of damage, such as cracks, dents, or scratches on the body of the power meter. Particularly, look for cracks in the area around the strain gauges, as damage to this part of the power meter is the most detrimental to its accuracy . Pay attention to the condition and shape of the mounting points and interfaces.
Functional testing
After the visual check is complete, proceed to functional testing. For a strain-gauge based power meter, this procedure simply involves performing a series of pedal strokes and verifying that the device reports them in A good practice is to compare the results received from the power meter in question to those obtained from a different power meter or to the expected result. For instance, a failing device may report completely random and bizarre mid-ride power values. However, it may be able to distort values so subtly they resemble real data points; this is where veryfing the power output is a valuable step.
Calibration and zero-offset procedure
After functional testing is complete, proceed to calibrate the device according to the manufacturer’s guidelines. Additionally, perform the zero-offset procedure and check if the power meter allows you to follow through with it . If the calibration results show that the device is no longer in optimal condition, it could have been physically damaged, compromising its accuracy. Regularly calibrating the power meter allows you to spot potential issues before they begin to have a marked effect on the data.
Software diagnostics and firmware updates
Check to see if your power meter’s manufacturer supplies any special software tools for checking the device’s health. Running these diagnostics can give you an in-depth look into any issues the power meter faces or confirm the hassle-free condition of the unit. The devices payload can also sometimes be mistaken for damage manifested in software: in that case, the device’s firmware might need an update.
Manufacturer evaluation
If you performed all of these steps and cannot guarantee accurate readings, send your power meter off to its manufacturer or an authorized repair center for an inspection. The company’s staff will have the tools and expertise needed to assess the scale of the damage and replace or repair all the relevant components in the device.